
Making shoes is a true CRAFT

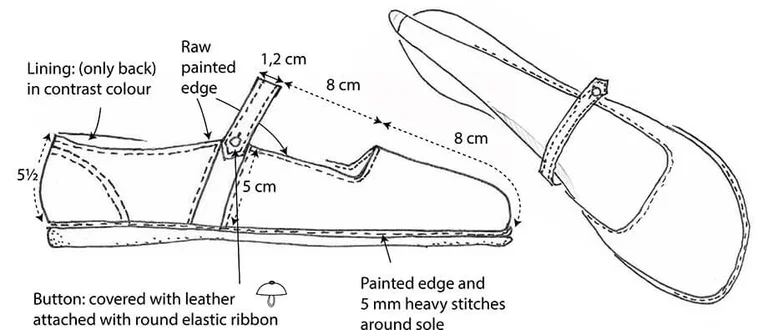
From sketch to prototype
A new shoe, last or sole always begins as a basic sketch. As designers, we know a great deal about function, materials and production options. When creating the sole, last and other features of a shoe, it’s essential to understand the actual manufacturing process. The leather can be smooth hide or tough nubuck. What should the sole look like? Is it a warm winter shoe or a lightweight lace-up? All the details need to be perfect on paper before production can begin.
Lasts and soles
Nowadays, the prototypes for lasts and soles are digitally produced and 3D-printed layer by layer. These used to be made out of wood by hand by a formier.
Cast in metal moulds
Liquid rubber is poured into a mould to make soles of all sizes. The soles can also be cut out from rubber or plastic blanks.
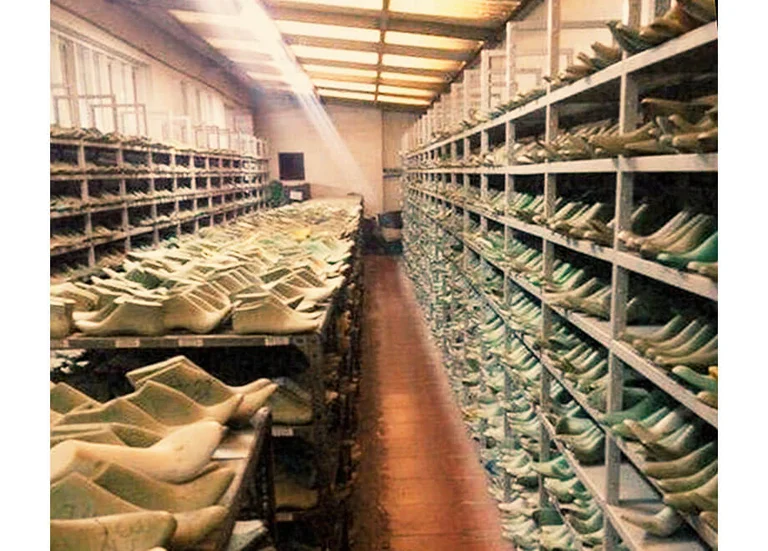
Rows of lasts
Our manufacturers store all lasts in methodical order. One foot for each style and size. We reuse our lasts over and over. Making new ones is expensive and time-consuming.
Cork soles
Blocks and sheets of cork are made into heels and soles. Cork comes from cork trees which grow in Portugal – locally produced! Each sole and heel is individually cut out using a bandsaw.
The leather is tanned & prepared
The tannery turns stiff rawhides (by-products of the meat industry) into beautiful, soft leather, suitable for making shoes and other leather goods. The tanning process takes place in large wooden barrels without the use of any heavy metals, such as chromium. It therefore complies with REACH, the EU’s legislative framework for chemicals, which has led to substantial improvements in tanning processes within the footwear industry. Tanning used to cause considerable harm to the environment.
Each shoe part is cut out
For each shoe design, iron cut-outs are made for each component of the shoe. Once the pieces have been cut, the shoes are stitched together and fitted with eyelets or straps. The stitched shoe is then placed on the last to stretch it to the shape and size of the last. Next, the finished rubber sole is attached.
Shoe factory in Portugal
Porto has long been home to numerous shoe factories. “Ours” is a medium-sized, family-owned factory with 105 employees. We’ve been working with Fernanda for many years. She is the contact person for our footwear production.