
Kengän valmistaminen – todellista KÄSITYÖTÄ

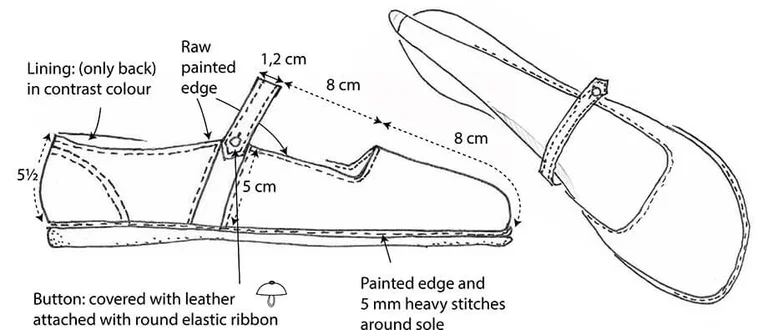
Luonnoksesta prototyyppiin
Uuden kengän, lestin tai pohjan tekeminen alkaa aina yksinkertaisesta luonnoksesta. Meidän suunnittelijoiden on aina ajateltava toimivuutta, materiaaleja ja valmistusmahdollisuuksia. Uuden kengän valmistuksessa ja erilaisten yksityiskohtien, kuten lestin ja ulkopohjan suunnittelussa, on aina erittäin tärkeää ymmärtää, miten valmistus toteutetaan. Nahka voi olla sileää nappaa tai vahvaa nupukkia. Millainen pohjan pitää olla?
Onko kyseessä lämmin talvikenkä vai kevyt nyörikenkä? Monien yksityiskohtien on oltava selvillä, ennen kuin tuoteluonnos on valmis.
Lesti ja pohja
Lestin ja pohjan prototyypit tehdään nykyisin digitaalisesti ja tulostetaan
kerros kerrokselta 3D-tulostimella. Ennen työ toteutettiin vieläkin enemmän käsityönä, koska puuseppä valmisti prototyypin puusta.
Pohja valetaan metallimuotissa
Sulatettu kumi kaadetaan kullekin pohjakoolle tehtyihin valumuotteihin. Pohja voidaan myös stanssata kumi- tai muovilevystä.
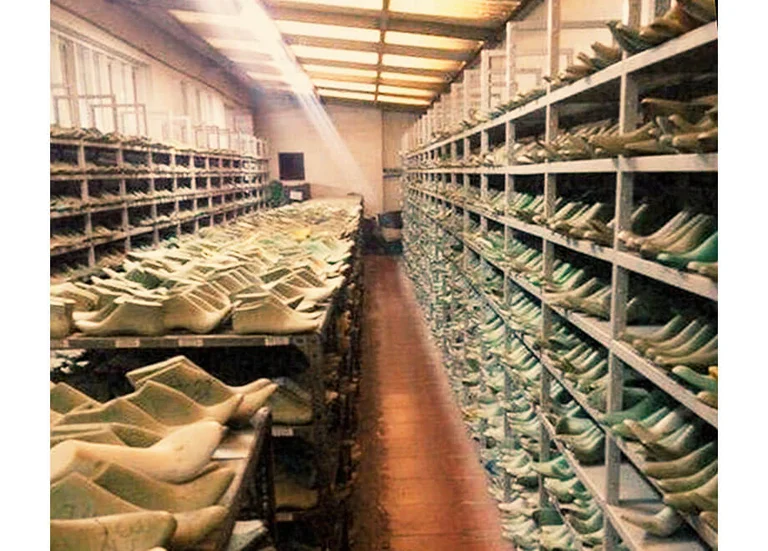
Lestivarasto
Valmistajilla ovat kaikki lestit varastoituina hyvässä järjestyksessä. Yksi jalka jokaisesta eri mallista ja koosta. Käytämme itse lestejämme useita kertoja, koska uuden lestin valmistaminen vaatii paljon työtä
ja rahaa.
Korkkipohja
Korkkipuusta saaduista korkkilevyistä tehdään kengänpohjia ja kantoja. Korkkipuu kasvaa Portugalissa – siis lähituotantoa! Jokainen pohja/kanta sahataan yksitellen vannesahalla.
Nahka parkitaan ja valmistellaan
Nahkurinverstaalla raakanahkat (lihateollisuuden jäännöstuotteita) muunnetaan jäykästä ja karkeasta nahasta pehmeäksi ja kauniiksi materiaaliksi, joka sopii kenkien tai muiden nahkatuotteiden valmistukseen. Parkinta tehdään isoissa puurummuissa ilman kromia ja raskasmetalleja EU:n kemikaalilainsäädännön REACHIN vaatimusten mukaisesti, mikä on saanut aikaan suuria parannuksia juuri kengänvalmistuksen parkinnassa. Aiemmin parkinta oli ympäristön kannalta erittäin vaarallinen osa valmistusprosessia.
Jokainen kengän yksityiskohta stanssataan
Jokaisessa kenkämallissa valmistetaan rautameisti kengän jokaista osaa varten. Kun osat on stanssattu, kenkä ommellaan ja siihen kiinnitetään vahvikerenkaat ja soljet. Sitten kenkä asetetaan lestiin venymään muotoonsa. Valmis kumipohja liimataan paikoilleen. Viimeisessä vaiheessa kenkä laitetaan uuniin, jossa se saadaan lestin avulla
halutun muotoiseksi.
Kenkätehdas Portugalissa
Portossa monet kenkätehtaat ovat toimineet jo pitkään. ”Meidän” tehtaamme on perheomisteinen, keskisuuri tehdas, joka työllistää 105 henkeä. Kenkäasioissa yhteyshenkilönämme toimii Fernanda, jonka kanssa olemme tehneet yhteistyötä monien vuosien ajan.